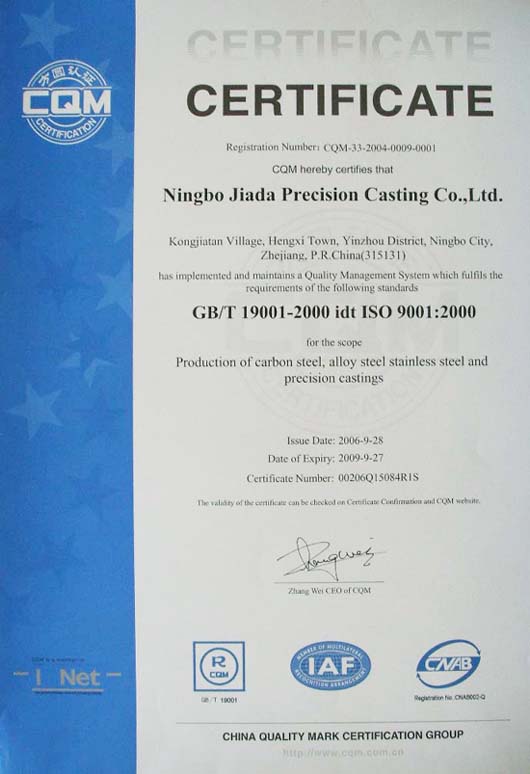
 
OUR QUALITY MANAGEMENT SYSTEM ISO 9001:2000 CERTIFIED
PROTOTYPE CONFIRMATION FROM CUSTOMER
- Before high volume production, we send prototype to customer for confirmation. Then seal the confirmed samples as the quality audit reference.
ADVANCED QUALITY/PRODUCTION PLANNING
- A Part Control Plan is generated for each part manufactured identifying all key product characteristics and defining the methods for their control.
- A Process Flowchart is generated and defines the manufacturing process as well as the interaction and controls throughout the product realization.
- Process Failure Mode & Effects Analysis is performed to assure the prevention of defectives through the manufacturing process.
- A Full Metrology Review of the key parameters is performed and methods established to assure design intent is met.
- A Full Dimensional Layout is performed to verify mold design and part print compliance in the pre-production phase.
MEASURING EQUIPMENT
- Spectrometer for Spectrographic Analysis of Alloy, Metallurgical Microscope for Microstructure Analysis, Universal Mechanical Property Tester for the Tensile/Yield Strength, Elongation Analysis.
- 2-Coordinate Measurement Machines for full dimensional layout
- Field Manager for real-time monitoring and analysis of key process parameters
- Standard calibrated instruments used throughout industry to verify key product characteristics
QUALITY CONTROL
- Part Qualification: First-Piece Inspection at the start of each production run
- Variable and Attribute Control Charting during the production run
- Part Evaluation: Last Piece Inspection at the end of each production run
- Final Audit: Random sampling of each ship lot for compliance of key characteristics
QUALITY ASSURANCE TEAM
- Experienced and dedicated engineers in Quality Engineering, Quality Auditing, Quality Technology, and Mechanical Inspection
- Our cross-functional approach to Quality is personified by Product Control Teams
- Internally Certified Operators demonstrate our commitment to Continual Improvement
 
|